120kg 견디는 안전화 깔창 소재 개발
섬유회사 성재엠에이치택
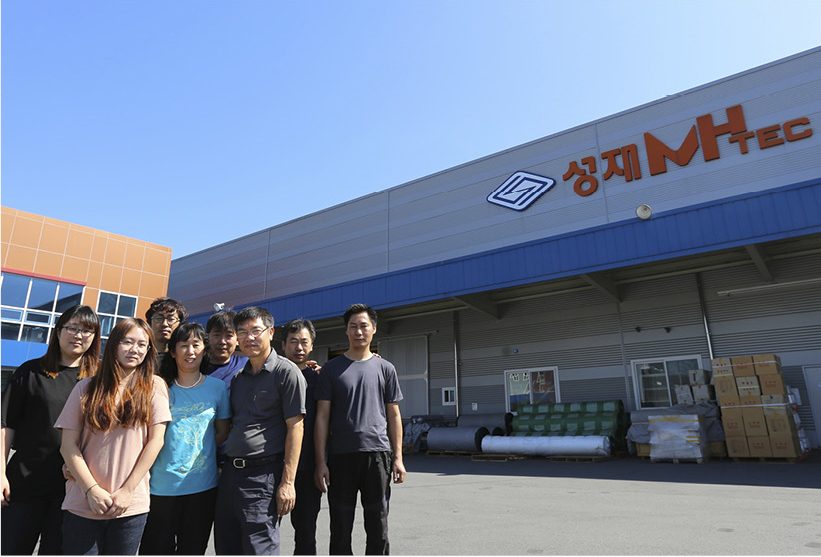
이탈리아산 원사로 제작하는 안전화 깔창 원단
안전화 밑창의 기본 구조는 이렇다. 땅에 직접 접촉하는 맨 아래에는 미끄러움을 방지하기 위한 고무 밑창이 있고 그 위에 날카로운 물체로부터 발바닥을 보호하기 위한 고강도의 원단이 들어가며 그 위에 사용자의 발바닥에 닿는 깔창이 들어간다. 섬유회사 성재엠에이치택에서 개발한 섬유 원단은 바로 밑창과 깔창 사이에 들어가는 고강도 원단이다.
과거에는 안전화에 스테인리스로 만들어진 철판이 들어가 땅바닥의 못으로부터 작업자의 발을 보호하기도 했다. 하지만 기본적으로 철판이 들어간 안전화는 신축성이 부족해 걸을 때 불편했고 게다가 오래 사용하다 보면 구부러졌다 펼쳐졌다 하는 부분이 깨져 그 사이로 못이 뚫고 들어올 가능성도 존재했다. 그래서 지금은 보통 폴리에스테르 섬유로 만들어진 원단을 사용한다. 성재엠에이치택 권성열 대표는 무엇보다 품질에 있어서는 빈틈이 없다 말한다.
“이탈리아에서 들여온 폴리에스테르 원사를 이용해서 120kg 무게를 견뎌낼 수 있는 고강도의 원단을 제조하고 있습니다. 품질에 대해서 빈틈이 없다 말할 수 있는 것이, 저희는 직접 품질 검사 기계를 갖추고 각 과정마다 검사를 진행하고 있기 때문입니다. 제가 아는 바로는 원단 제조하는 회사 가운데 직접 검사 기계를 갖고 있는 회사는 저희 밖에 없을 겁니다. 그만큼 품질에는 자신있습니다.”
2년 전까지는 안전관리공단에서 안전화 완성품의 검사 뿐 아니라 원단 회사의 원단도 검사도 진행했었다. 하지만 작년부터는 완성품이 아니면 검사가 불가능하다. 그래서 대표는 직접 검사 기계를 구입해 검사 과정을 진행하는 것이다.
“안전화 깔창은 안전기준 하에서 짜는 거니까요 항상 일정한 품질을 유지하는 것이 관건입니다. 똑같은 소재를 사용하더라도 제직시의 밀도라든지 두께라든지, 이런 게 항상 문제가 생길 수 있는 거거든요. 제직부터 마지막 제품이 나올 때까지의 작업 관리가 최우선적으로 필요한 것입니다. 저희는 그런 시스템을 갖추고 있습니다.”
4~5억원 하는 직기 수십 대 보유… 투자에 대한 열정
가격이 만만치 않은 품질 검사 기계를 구입하는 것은 기술에 대한 투자다. 권성열 대표의 기술 설비에 대한 투자 의지는 무엇보다 갖추고 있는 섬유 직기(織機)에서 완연히 드러난다. 현재 성재엠에이치택에서 갖추고 있는 직기는 스위스 독일 이탈리아 등에서 생산하는 첨단 직기다. 한 대에 4~5억원씩 하는 직기를 회사는 무려 30여 대나 보유하고 있다. 기술력 확보를 위한 대표의 투자다.
“은행에 빚을 져서라도 설비에 투자합니다. 1992년 맨 처음 공장을 지었을 때부터 지금까지 설비에는 끊임없이 투자해 왔습니다. 지금 보면 옷을 짜는 의류 직기는 최고 좋은 게 9천만 원 정도입니다. 그런데 누가 3억 짜리 5억 짜리 섬유 직기를 들여놓겠습니까. 하지만 저는 최고의 원사는 최고의 직기로만 직물을 짤 수 있다는 것을 알고 있습니다. 이탈리아에서 들어온 최고급 폴리에스테르 원사는 역시 첨단 직기가 아니면 짤 수 없는 겁니다.”
이탈리아산 최고급 원사가 있고 해외에서 들여온 최첨단 직기가 있다. 그렇다면 그것만 있으면 누구나 다 120kg을 견딜 수 있는 원단을 제조해 낼 수 있는 걸까? 대표는 거기에 한 가지가 더 있기 때문에 가능하다 말한다. 바로 성재엠에이치택이 가지고 있는 사반세기 동안의 제직(製織) 노하우가 바로 그것이다.
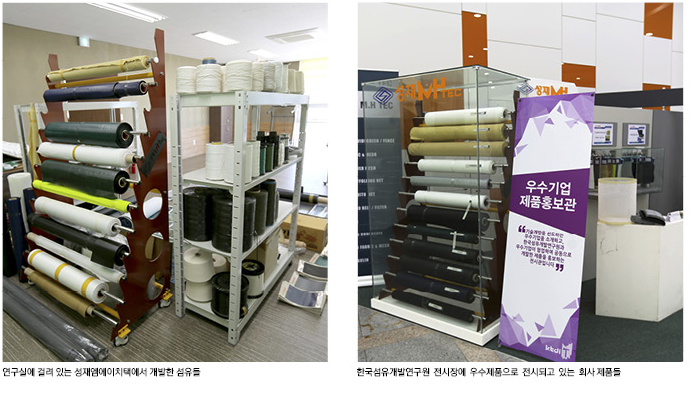
친환경 접착제 사용으로 발에 안전한 원단
성재엠에이치택이 자랑하는 여러 가지 제직 노하우 가운데 대표적인 기술은 여러 장의 원단을 붙이는 합포 기술이다. 보통 100kg이상의 무게를 견디는 원단은 세 장에서 네 장의 원단이 부착되어 만들어진다. 그 과정이 굉장히 중요한 것이다. 요즘은 과거와는 달라서 무조건 딱딱하게만, 야무지게만 붙인다고 되는 일이 아니다. 부드러우면서도 친환경적이 될 수 있도록 소재 사용이 필요하다.
“위에 깔창이 들어가긴 하지만 그래도 발, 사람의 몸과 가깝게 들어가는 거잖아요. 그런데 안전화는 오래 신다 보면 땀이 나게 됩니다. 그러면 합포시의 접착제가 인체에 안 좋은 성분이 있으면 발에 문제가 생길 수도 있잖아요. 깔창 바로 아래에 들어가니까. 그런 것들도 다 챙겨야 하는 겁니다.”
뿐만 아니라 다른 섬유 업체에서 만드는 원단에는 밑창의 고무와 잘 붙게 하기 위해 합포시 맨 윗장에 얇은 면 한 장을 더 붙이는 것이 보통이다. 하지만 성재엠에이치택은 면을 붙이지 않고 원단과 밑창을 바로 붙일 수 있는 기술을 개발했다. 덕분에 두께도 얇아지고 뻣뻣함도 줄어들었다. 하지만 회사의 입장에서 가장 큰 이점은 바로 작업 공정이 줄어들어 비용을 절감했다는 것이다.
“원단이든 공구든 우리나라에서 뭐든 제조를 하려면 항상 중국이 문제잖아요. 중국산의 낮은 가격. 품질적인 면에서는 월등하지만 가격 경쟁력도 필요하겠죠. 저희는 설비에 투자를 더 해서 생산량을 늘릴 계획을 가지고 있습니다. 그렇게 해서 단가를 낮추려고요. 어떻게 해서는 가격적인 면에서도 경쟁력을 갖추어 나갈 생각입니다.
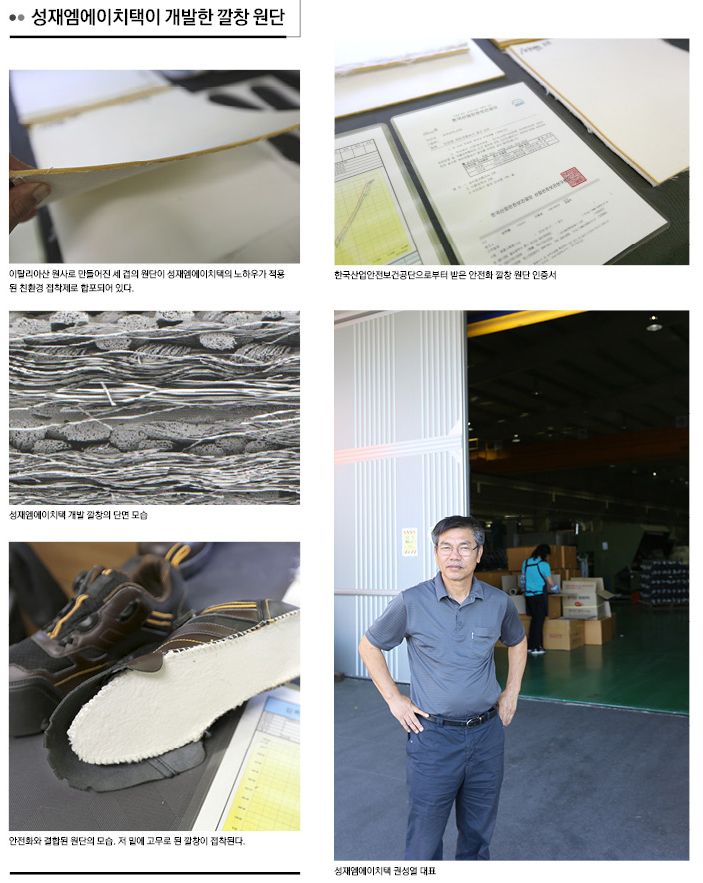
안전화 뿐 아니라 방충망으로 공구계 접근 중
성재엠에이치택의 제품은 그 기술력을 인정받아 대구시 서구 소재 한국섬유개발연구원 1층 전시장에 우수제품으로 전시 중이다. 그만큼 국가로부터도 인정받고 있는 것. 회사는 안전화 깔창 원단 뿐 아니라, 우리나라 산업에 필요한 거의 모든 섬유를 만들고 있다. 국내 다양한 산업 현장에서 사용되고 있는 성재의 섬유 제품들. 하지만 권성열 대표는 국내 판매에 만족하지 않고 세계 시장에 진출하려는 욕심을 가지고 있다.
“해외 전시회에 많이 출품하고 있습니다. 지난 5월에는 독일의 종합 산업용 안전 전시회인 텍스텍에도 나갔었고 9월에는 미국 산업용 종합 전시회에 출품했습니다. 저희 공장에서 나오는 거의 모든 섬유 제품을 가지고 가고 있어요. 작년 두바이에서 열린 세계 건축 박람회에도 제품을 출품했습니다. 올해 11월과 내년 1월에도 미국 전시회에 참가할 계획을 갖고 있습니다.”
과거, 우리나라 경제발전의 역군 중 하나였던 섬유산업은 지금 많이 가라앉아 있는 상태다. 하지만 대표는 계속해 노력을 하고 연구를 하면 돌파구는 나오기 마련이라 말한다. 안전화 깔창 원단 말고도 찾고 있는 공구 관련 돌파구 중 하나는 바로 플라스틱 모노 방충망이다. 벌써 2~3년 전쯤부터 공구상을 운영하는 사람들에게 대리점을 모집해서 판매 중이다. 전까지는 스테인리스 방충망 혹은 알루미늄 방충망을 사용하던 소비자들의 인식이 가격도 저렴하고 갈기도 쉬운 플라스틱 방충망 쪽으로 전환되고 있는 것이다.
앞으로 성재엠에이치택의 제품을 더 쉽게 공구상에서 찾아볼 수 있길 기대해 본다.
글·사진_이대훈